A SURE FOOTING AT WORK FOR 20 YEARS
Our safety shoes cover the entire range of our customers from industry. For example, an automobile manufacturer has very different requirements for safety shoes, from welding and metal processing, assembly and logistics, right through to the office sector, which we all meet.Customers include specialist retailers throughout EU as well as corporations and small to medium-sized companies from the automotive, construction and chemical industries as well as energy suppliers.
LEATHER UPPERS
We has been producing the leather uppers for safety shoes in its own factory. We have our own stitching team with years of working experience. In the past eleven years the company has increased the number of employees of stitching workers more than tenfold from an initial 10 to over 1,20 employees. All the uppers, i.e. the upper parts of the shoe without soles, are fully manufactured by us.
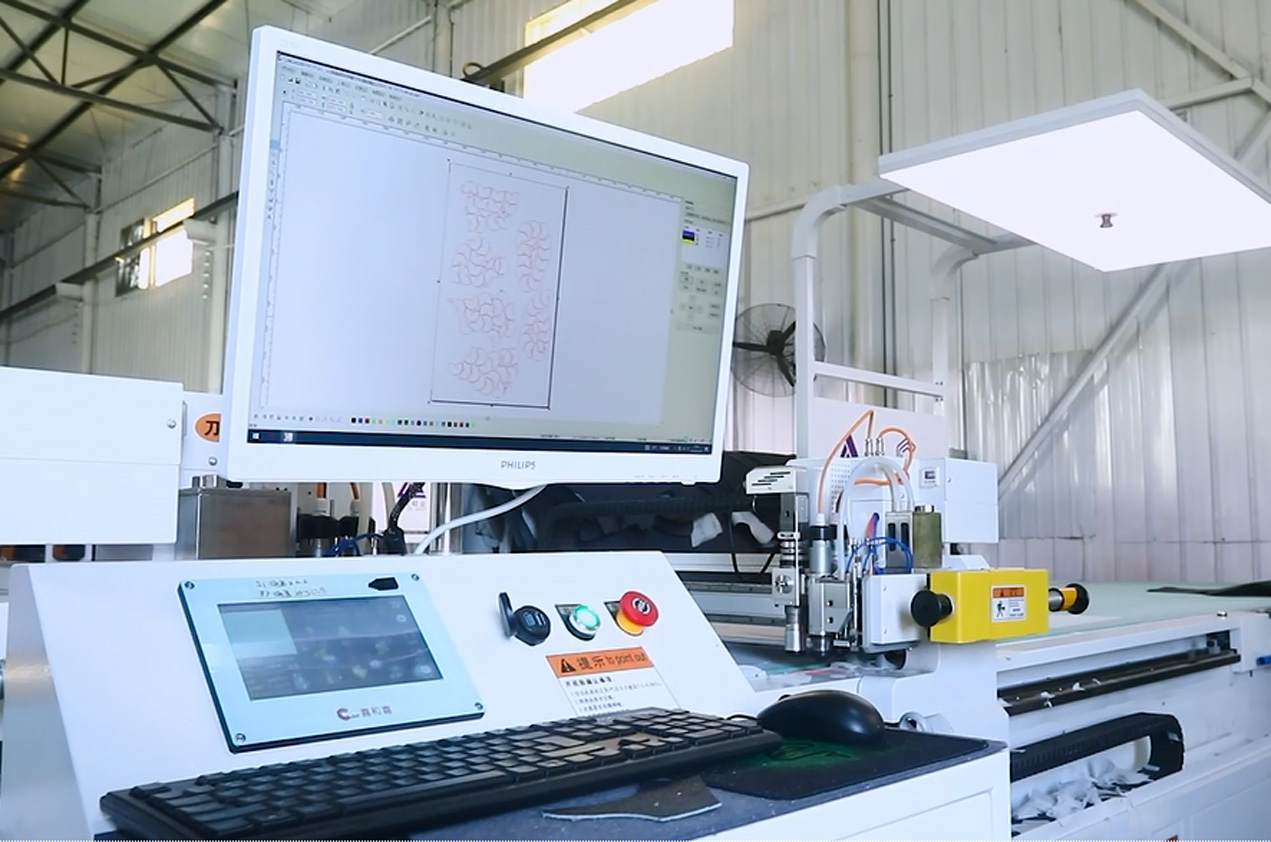
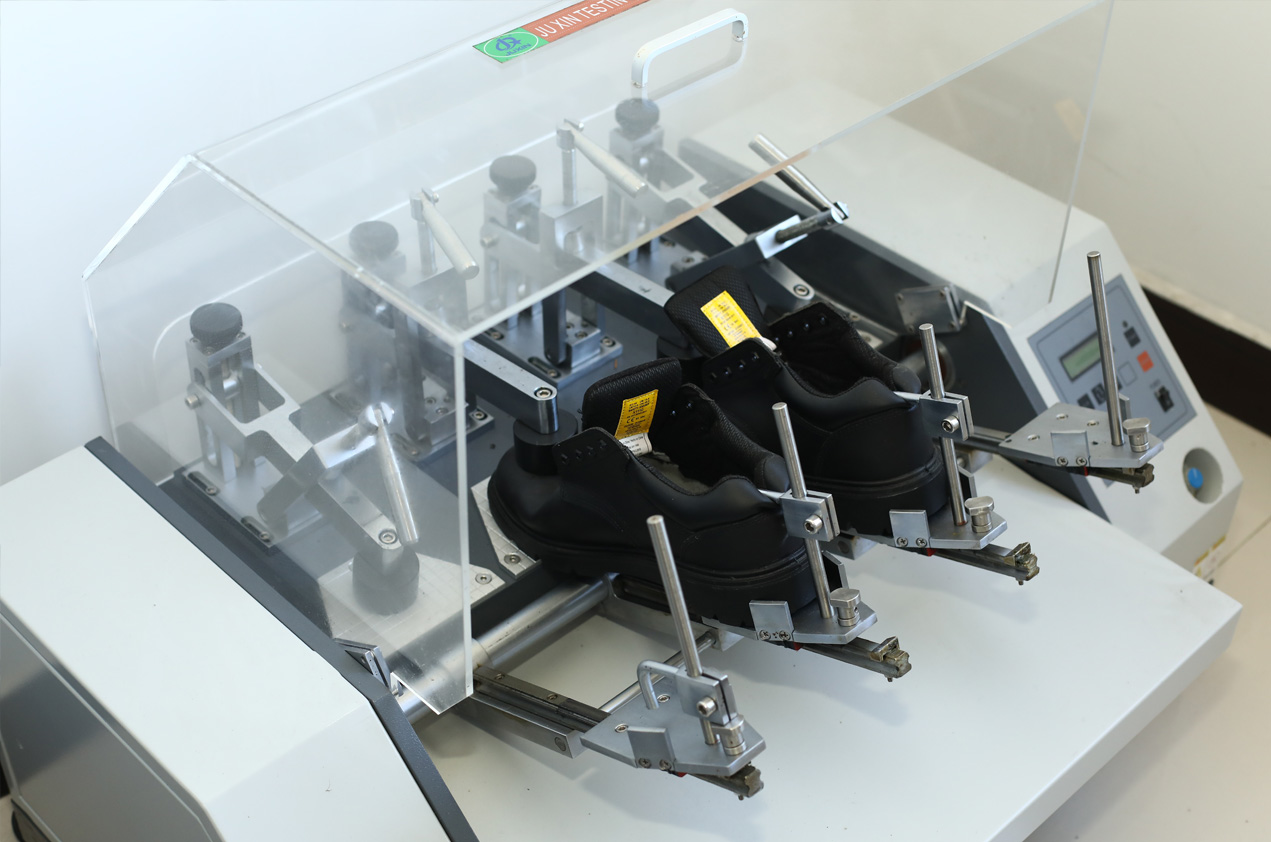
The production in Handan works in three shifts, 24 hours a day and six days a week. Here the shoes are provided with soles and given the final touch. A total of five high-tech PU soling machines have been available since 2023. Logistics, field service and financial accounting are also located in Handan. All marketing activities are controlled from here.
CONTINUOUS GROWTH
LUAN ® is growing continuously. In the last ten years the company has doubled its sales. Construction on the company premises in Wickede continues on a regular basis. A newly built hall was put into operation only three years ago. Currently, the new LUAN ® 4.0 building is due to open in winter 2020. The new complex is being created on an area of 3,500 m² for around 60 employees from final assembly. Social rooms and additional office space for back-office staff, which can be used in a carbon-neutral manner, will also be built. Modern heating systems without fossil fuels are used in everyday work without impacting the climate. In sales LUAN ® works with specialist retailers throughout Germany and also operates branches in the Netherlands, Denmark, Hungary and Poland. The company is also represented in all European countries. The export quota is approximately 25 percent.
THE KEY TO SUCCESS
While many manufacturers have moved to South-east Asia, we have continued to rely on the Handan location for our shoe production, final assembly and technology development. The company relies on consistent quality assurance from A to Z.
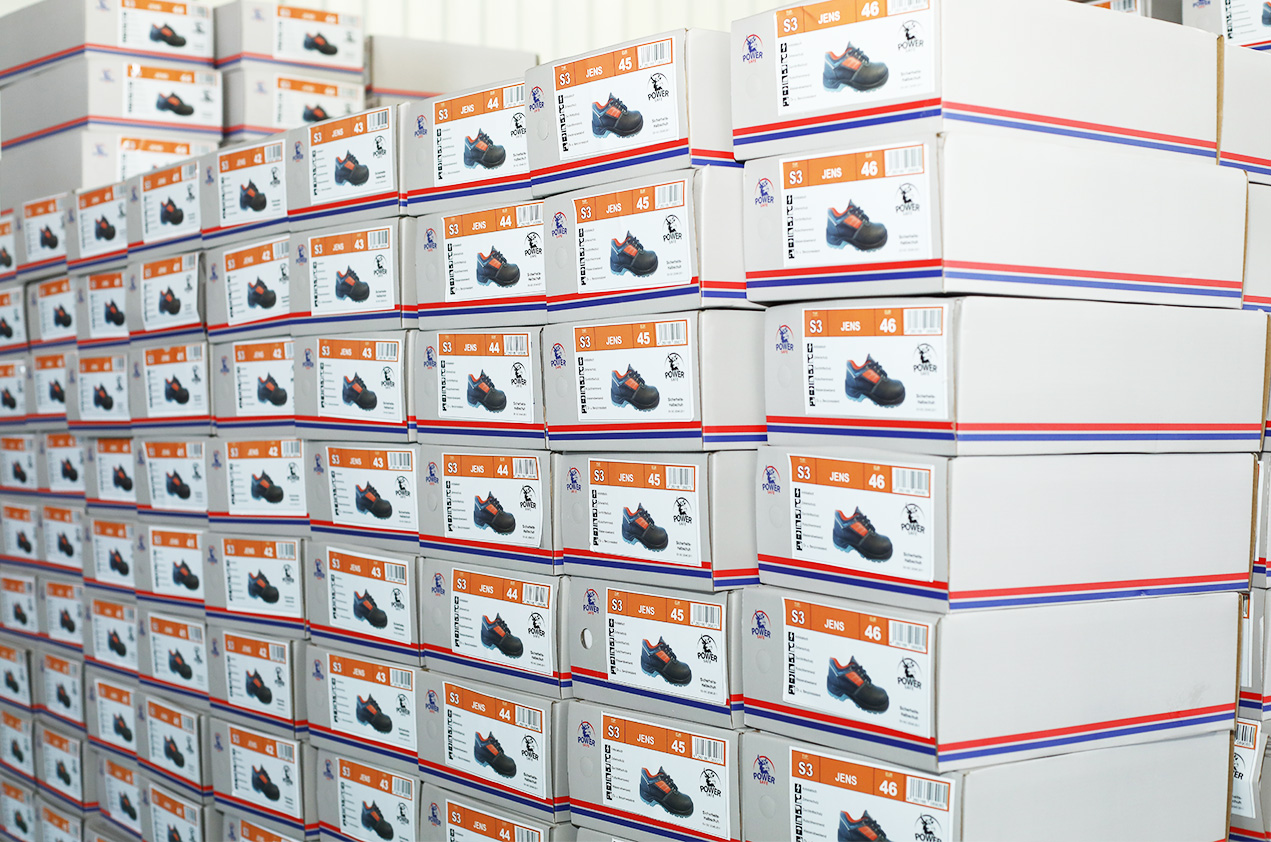
“In our factories we ourselves approve every leather skin, every microfibre material, every outsole and process everything there ourselves. This means that we are extremely flexible in production and are also able to cope with order peaks. We are close to the process, close to the customer and in this way we can implement innovations quickly, test them ourselves and put them into practice in our production."
As far as shoes are concerned, industry demands safety, comfort and ergonomics. Occupational health prevention is becoming more and more important. Employees should be protected from adverse effects on their health. Companies calculate the downtime of their employees. Expensive staff shortages, for example due to musculoskeletal disorders, should be avoided as far as possible. LUAN ® works with customers to develop new products that are precisely tailored to their needs.
For example, an automobile manufacturer in Germany was looking for a metal-free shoe for its transparent production line. Metal eyelets on the shoe should be replaced so that they can no longer scratch the paintwork. The fitters should be able to move flexibly in the new safety shoes even when kneeling. The "CF Series" was put into effect together with the customer. The automobile manufacturer's safety engineers and company doctors and the experts from LUAN ® shoe factory worked hand in hand.

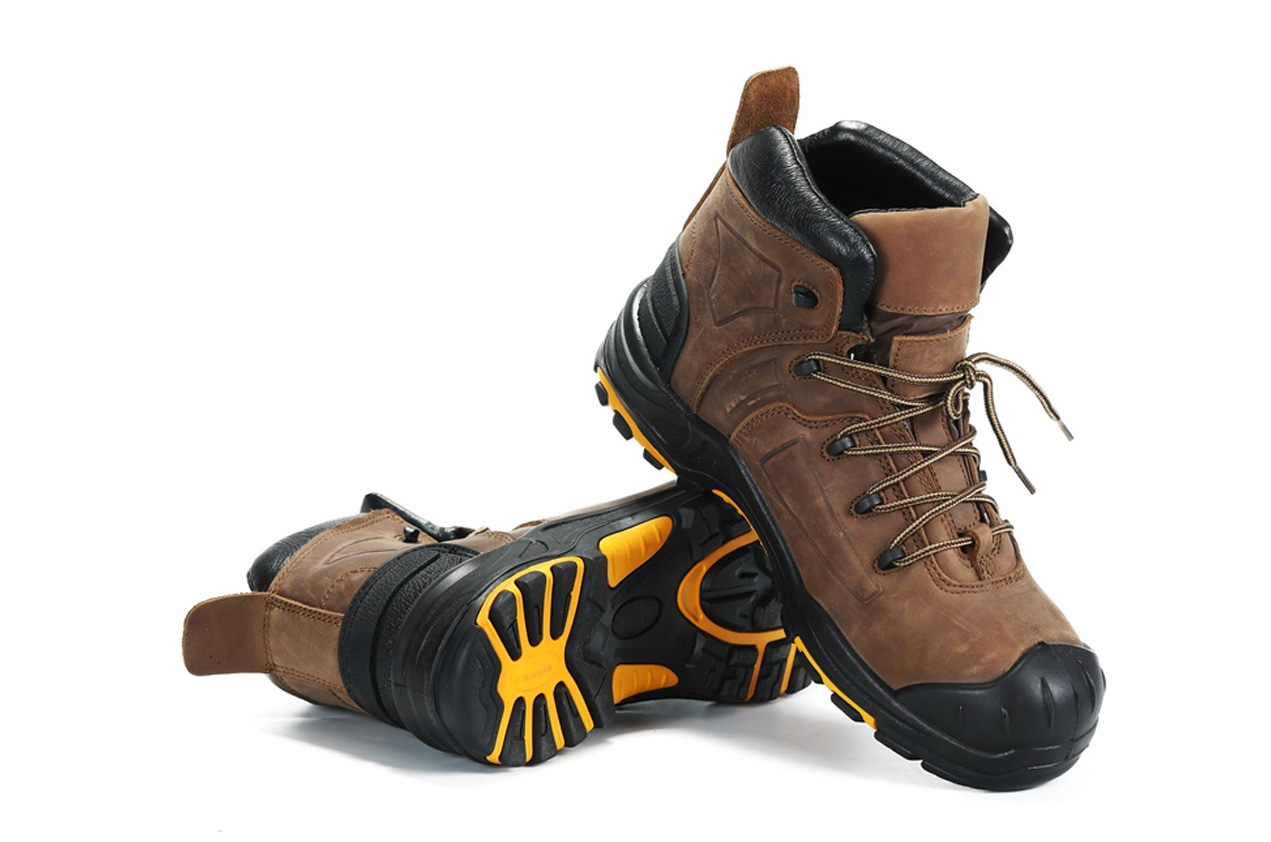
LUAN ® has designed a new work shoe, which prevents accidents with twisted ankles, for employees of the energy company Which climb high electricity pylons every day. The employees now benefit from improved ankle protection which is achieved by a second lacing on the shoe. The customer also attached importance to a good insole and an optimal fit: “Safety shoes have to fit perfectly. A foot scanner that we developed in-house enabled us to measure the length and width of the employees' feet exactly and thus determine the optimal shoe size for each individual employee"